Aside section
Cases
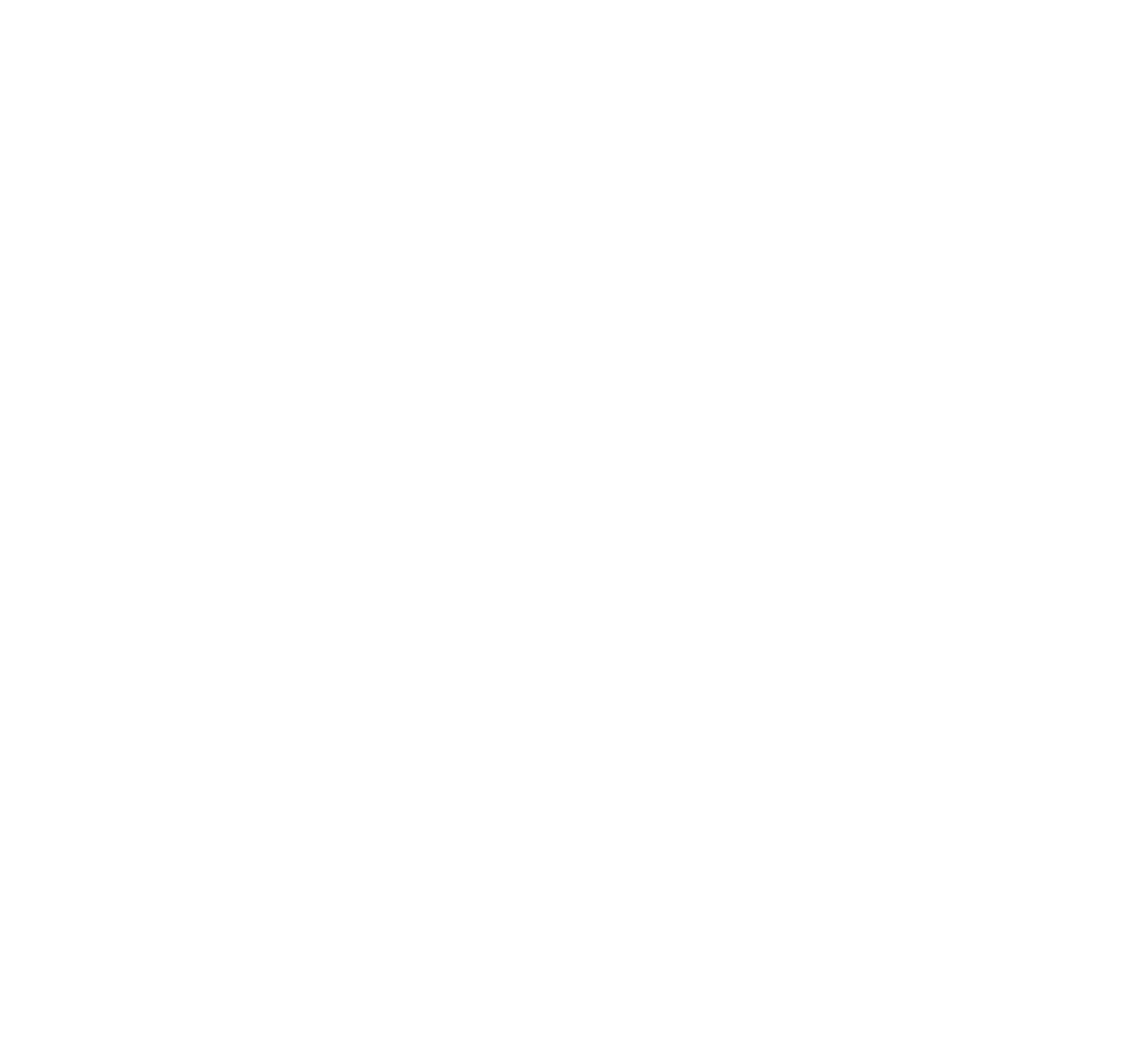
How industrial enterprise Interipe holding reduced the equipment downtime by 30% with IT-Enterprise.EAM
Implementation of IT-Enterprise.EAM system let Interpipe holding to reduce maintenance costs, carry out production equipment repairs based on information about their current condition, ensure high reliability of equipment operation with preventive repairs where failure probability becomes high.
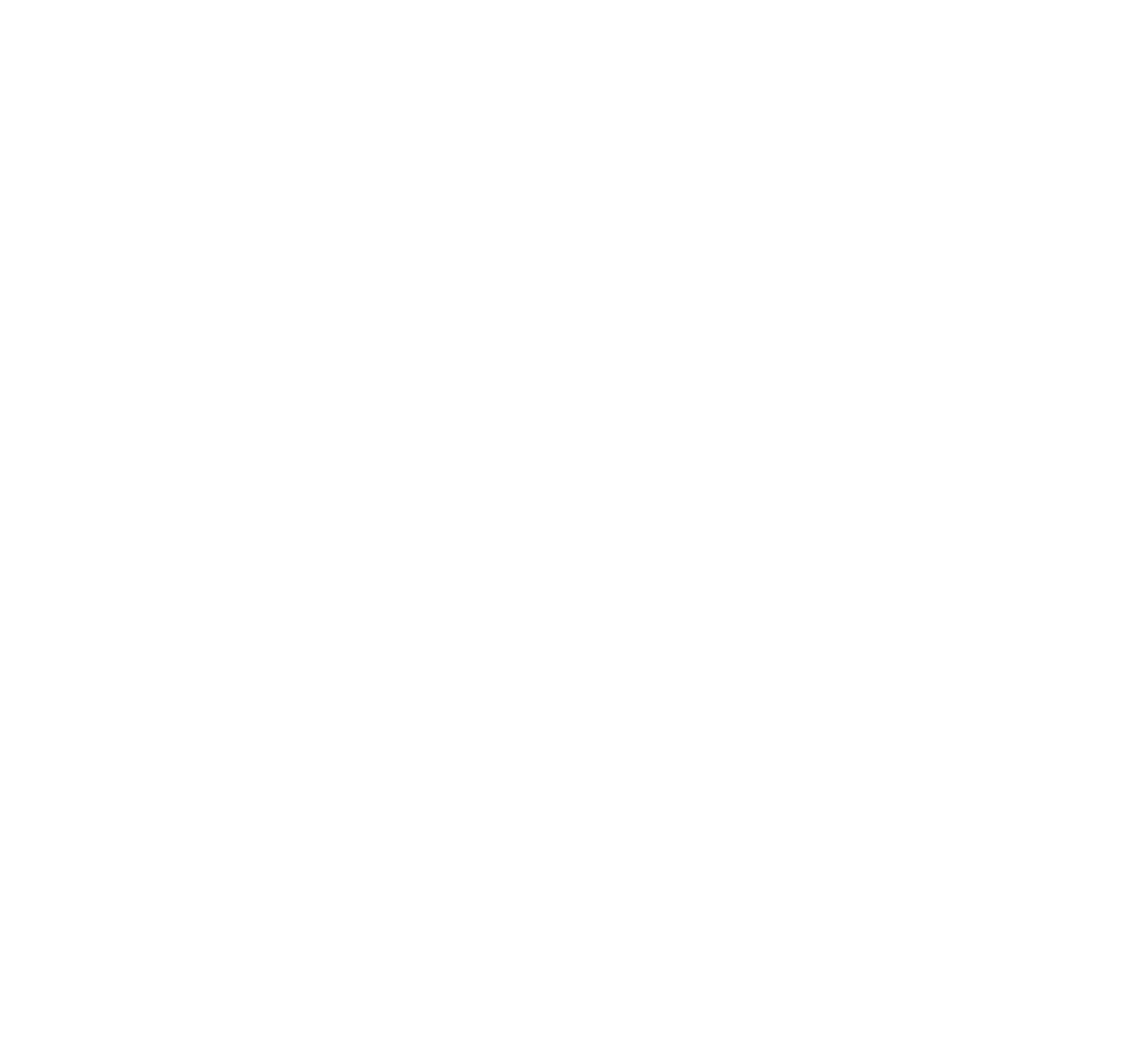
Interpipe's digital transformation of manufacturing
Interpipe is an integrated pipe and wheel company, a member of the TOP 10 list of the world’s largest seamless pipes’ producers.
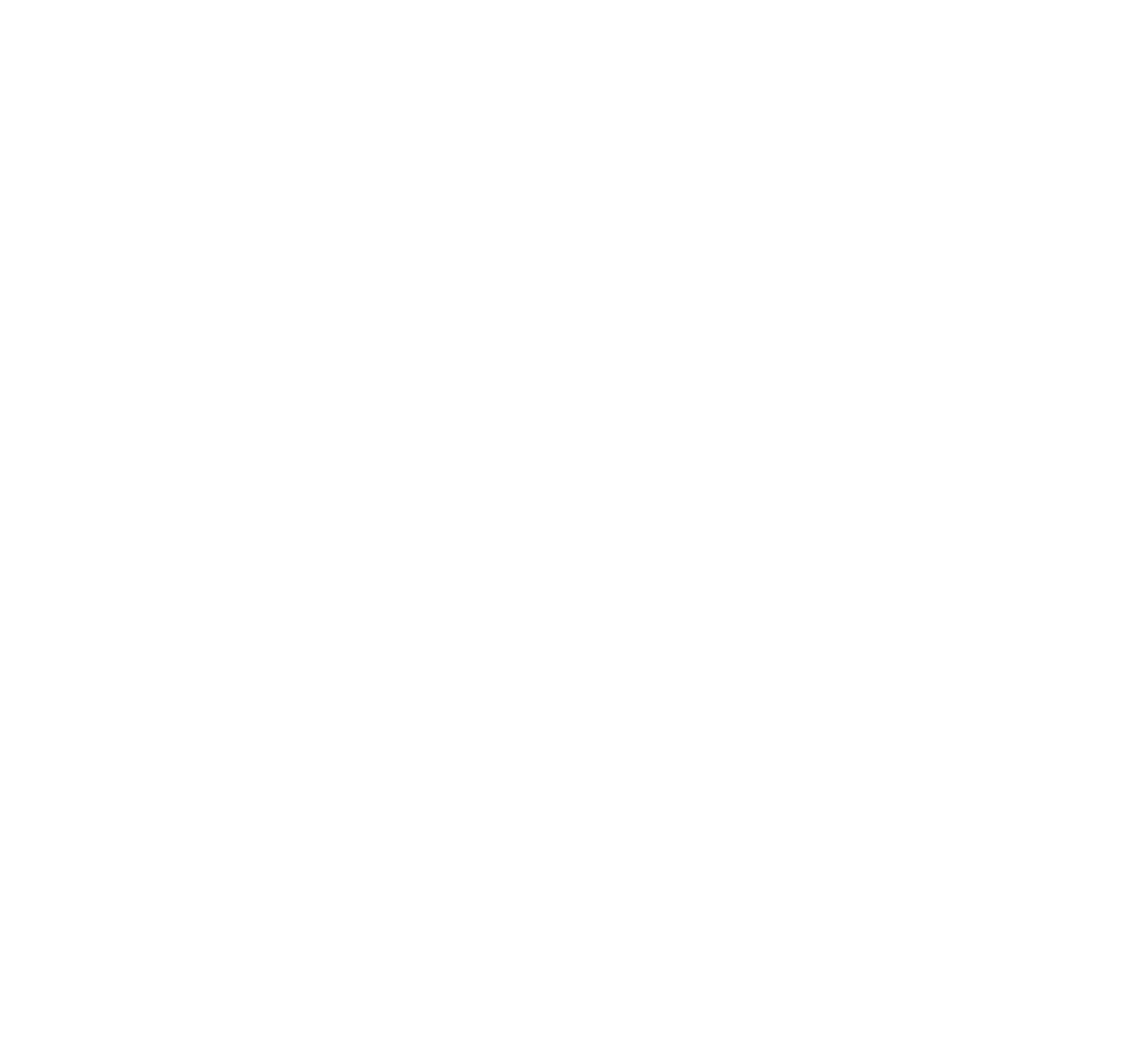
Improving the predictability and manageability of the enterprise due to the cost accounting in production Lviv Locomotive Repair Plant
Reduction by 15-20% of critical repairs cycles to the Lviv locomotive repair plant (LLRZ) due to the implementation of operational accounting of production costs on the basis of IT-Enterprise
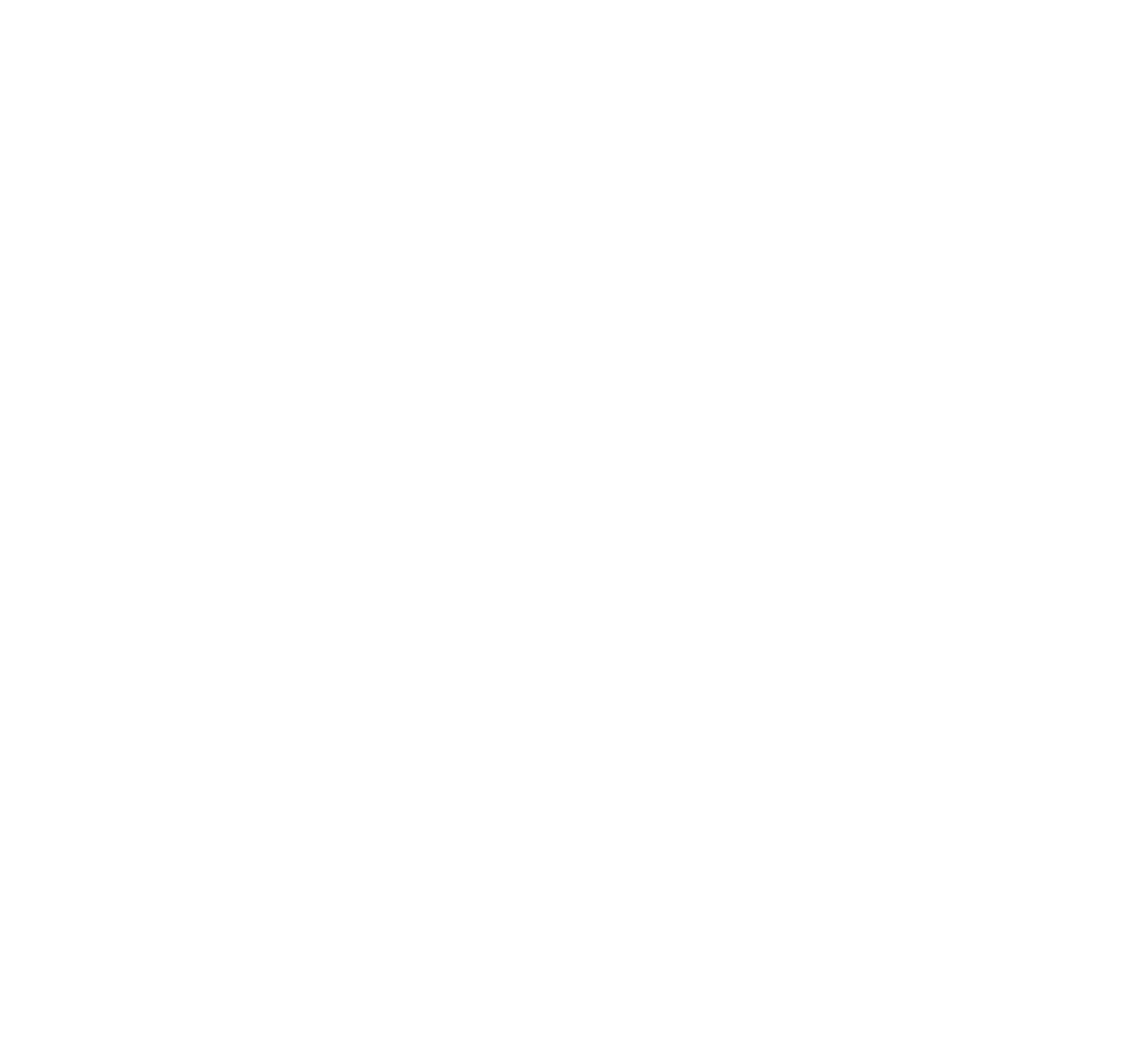
Optimal recruitment with IT-Enterprise.Recruitment
Optimal recruitment organized at the large industrial enterprise "Interpipe" with the help of IT-Enterprise solution.
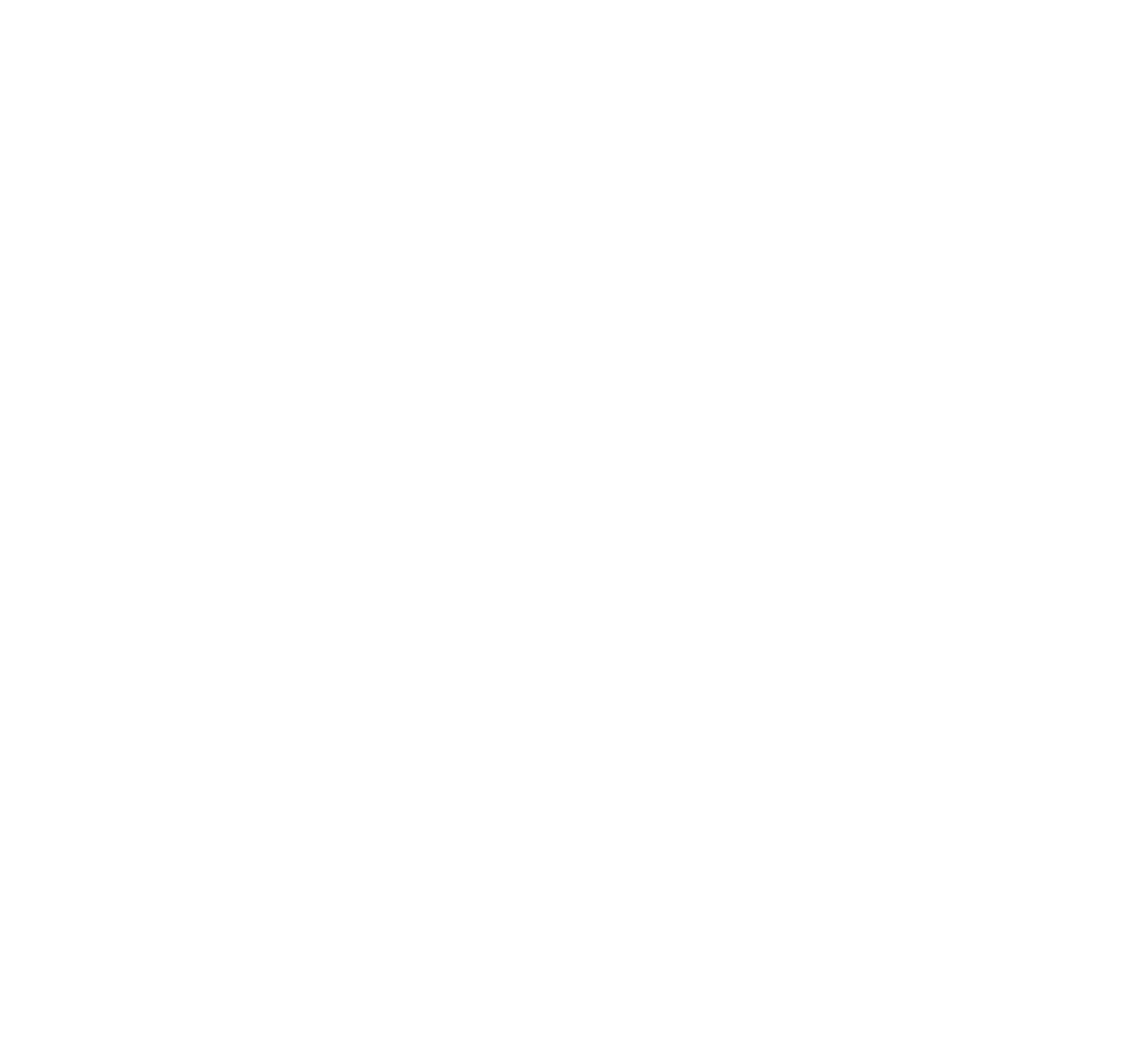
SmartFactory by IT-Enterprise – a platform for sustainable development of Interpipe
Due to the implementation of the SmartFactory by IT-Enterprise, industrial holding "Interpipe" reduced the storage costs of materials, reduced the risk of breaking schedule routine and failure of the orders timing, improved the rhythm of the production, and significantly reduced equipment downtimes.
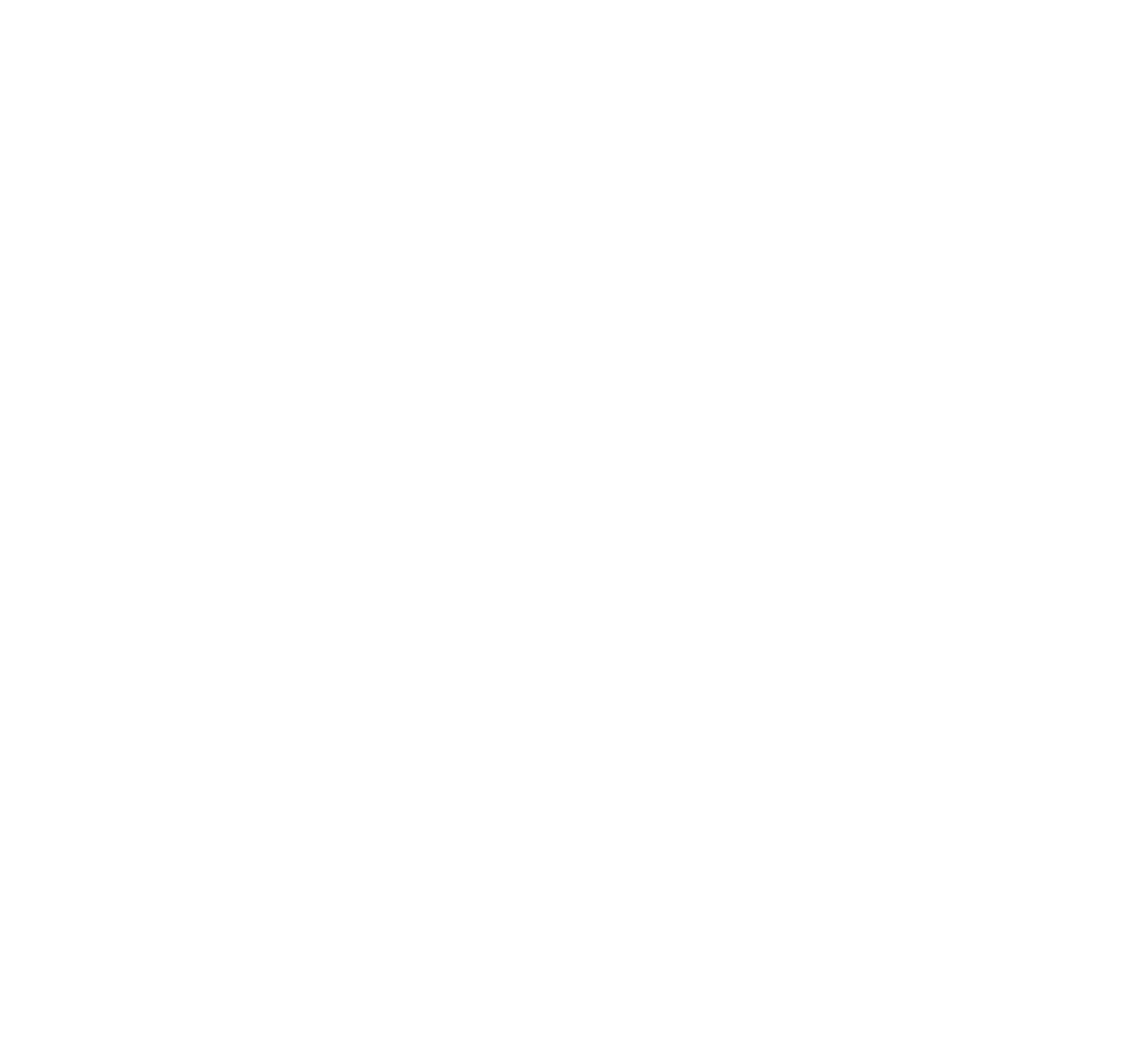
Unified treasury o Interpipe holding based on IT-Enterprise ERP-solution
As a result of the project of the Unified Treasury at Interpipe, financial divisions disbanded and a single Treasury were created. Now all payments are executed from the central managing company.
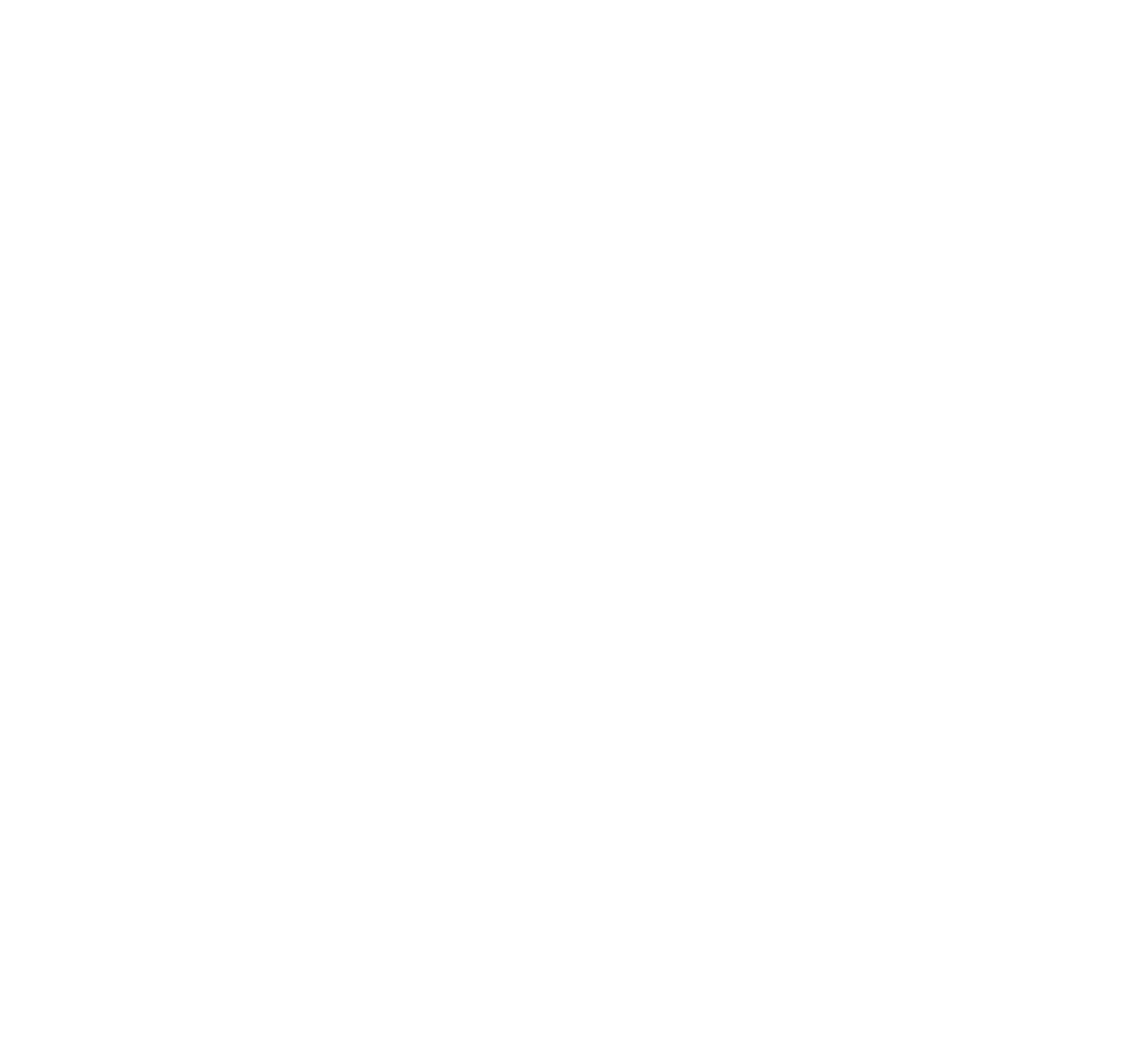
“Kovalska” industrial and construction group: 2 times loss reduction because of using incorrect norms
How the industrial-construction group "Kovalska " reduced costs and eliminated the use of incorrect norms due to the implementation of IT-Enterprise
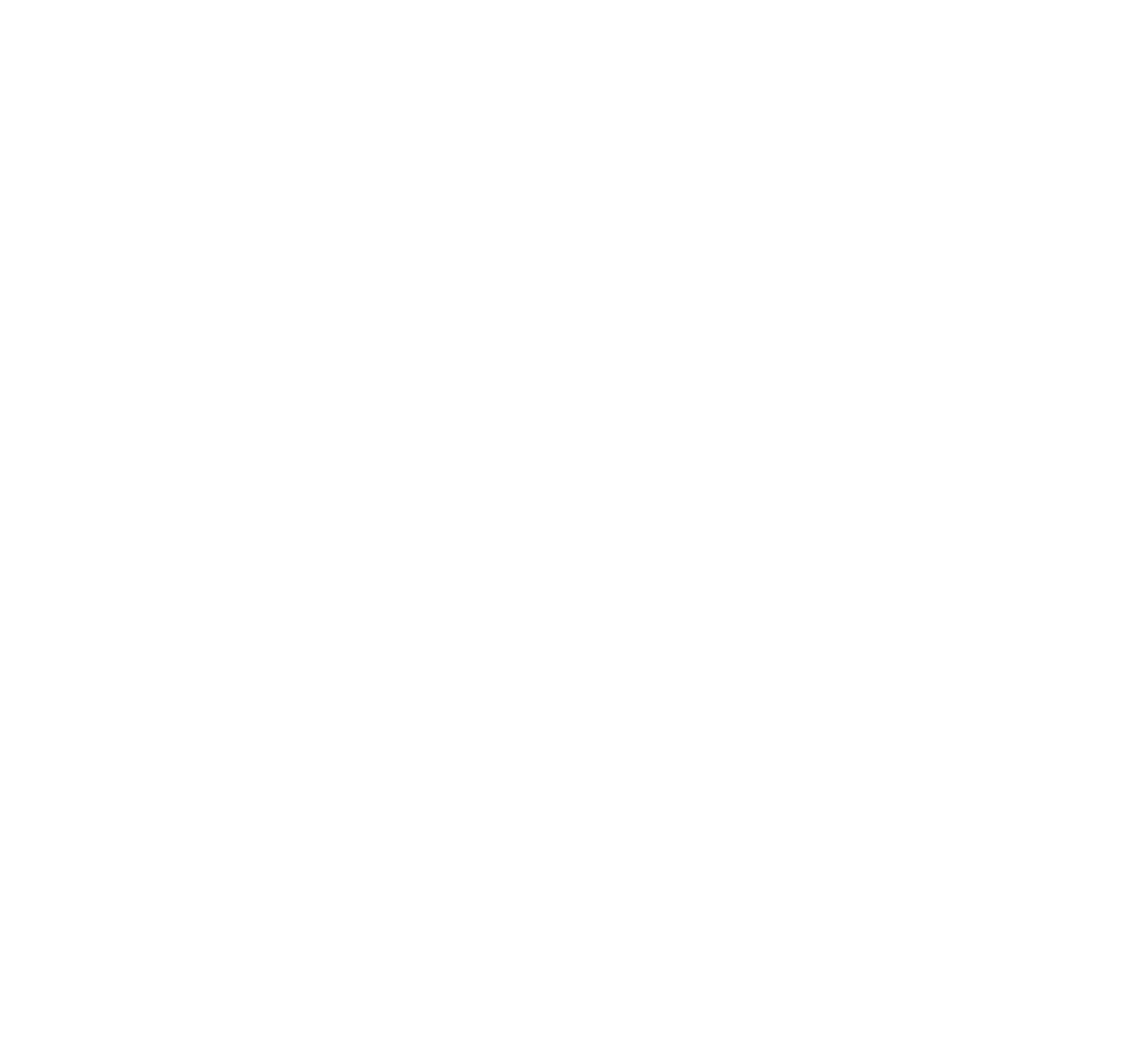
Work-in-Progress at Kremenchuk Wheel Plant Reduced by 15% with Operational Production Planning
How the Kremenchug Wheel Plant reduced the volume of work in progress by 15% due to the operational planning system implementation based on the IT-Enterprise ERP system
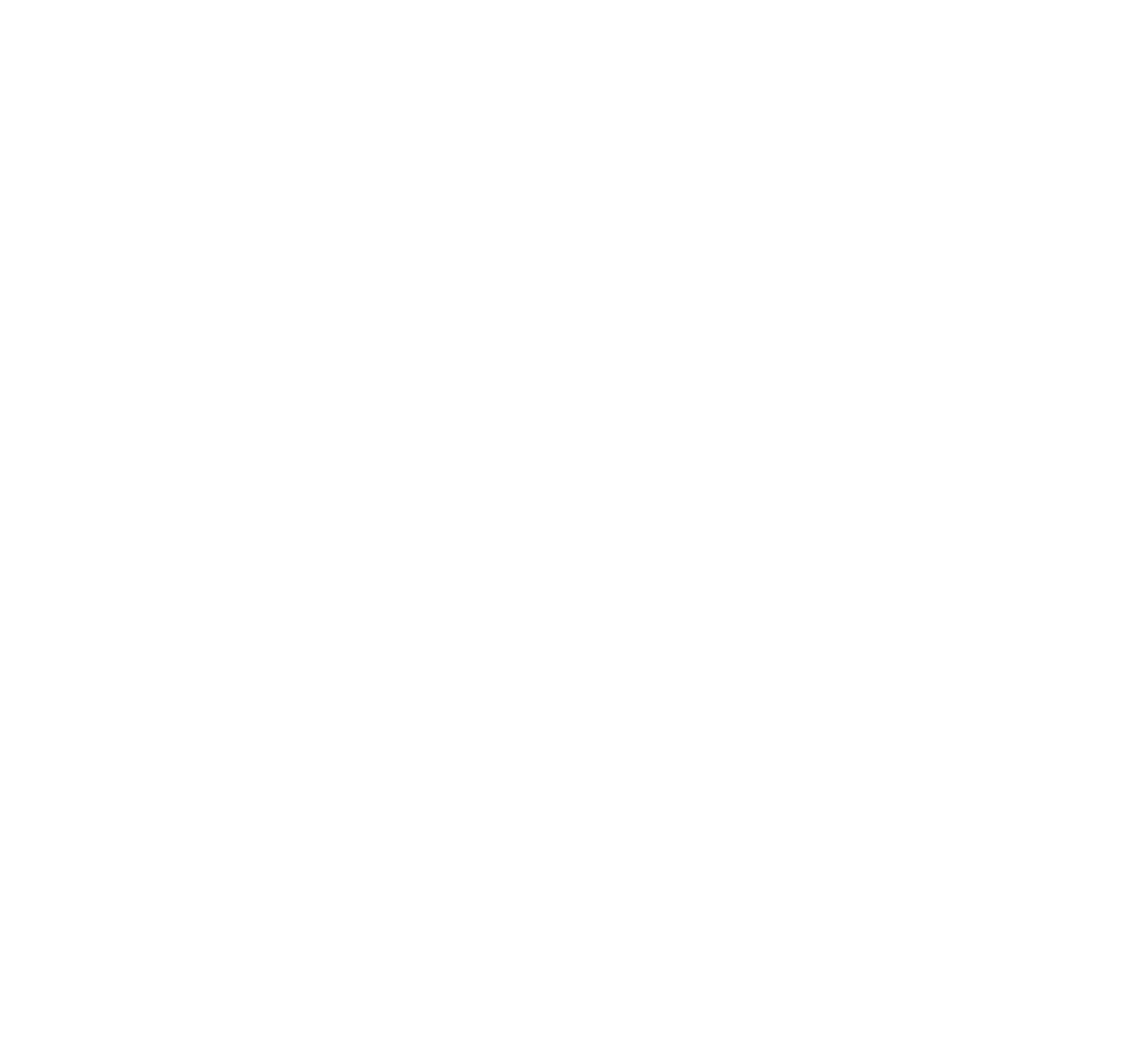
The expenses of the auto complex at the Poltava Mining and Processing Plant are controlled by IT-Enterprise
Due to automation of cars departure planning and account technical readiness, staff of dispatchers at Poltava GOK was reduced by half; the formation of accompanying documents is also automated.