Aside section
Cases
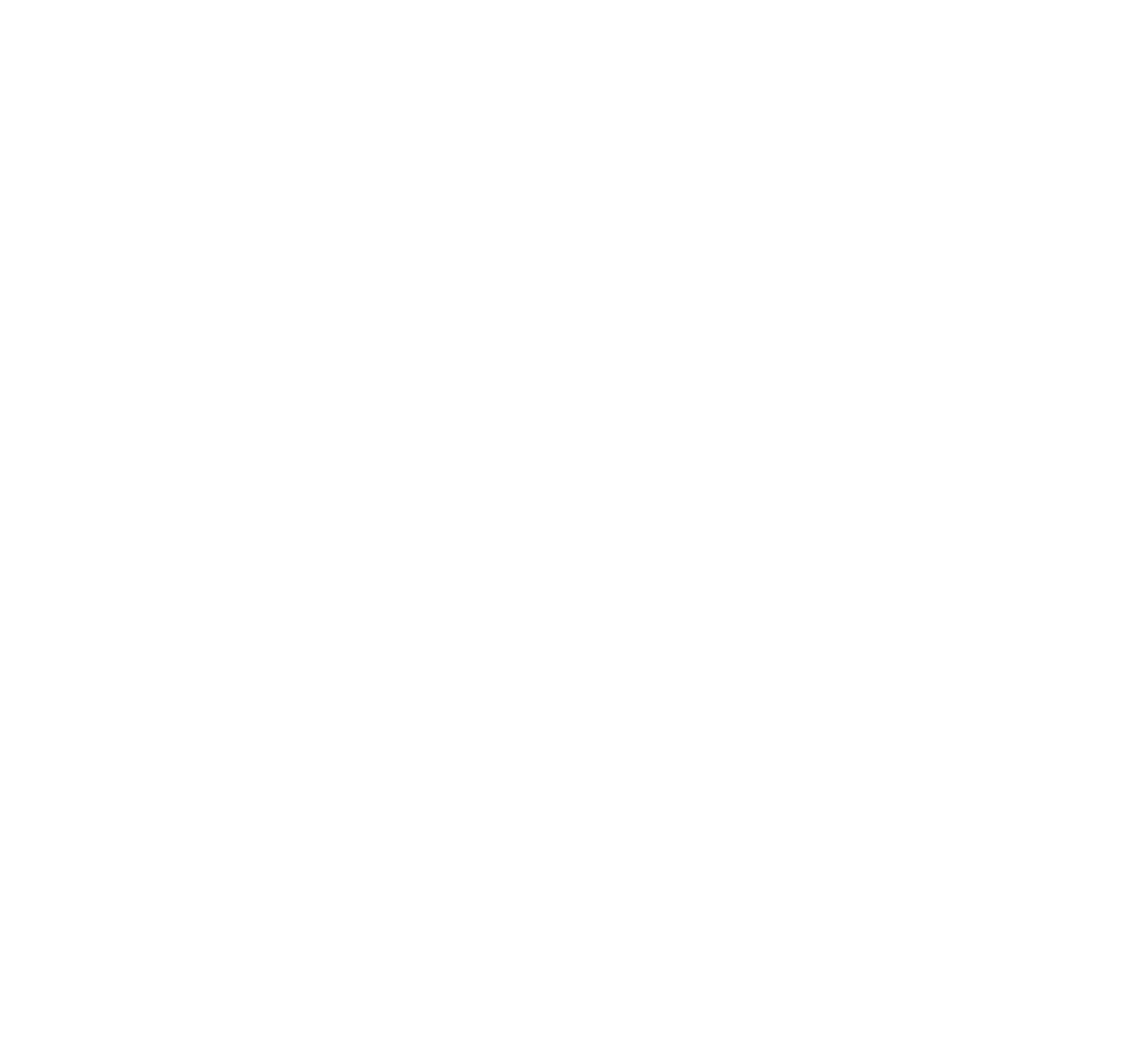
Interpipe's digital transformation of manufacturing
Interpipe is an integrated pipe and wheel company, a member of the TOP 10 list of the world’s largest seamless pipes’ producers.
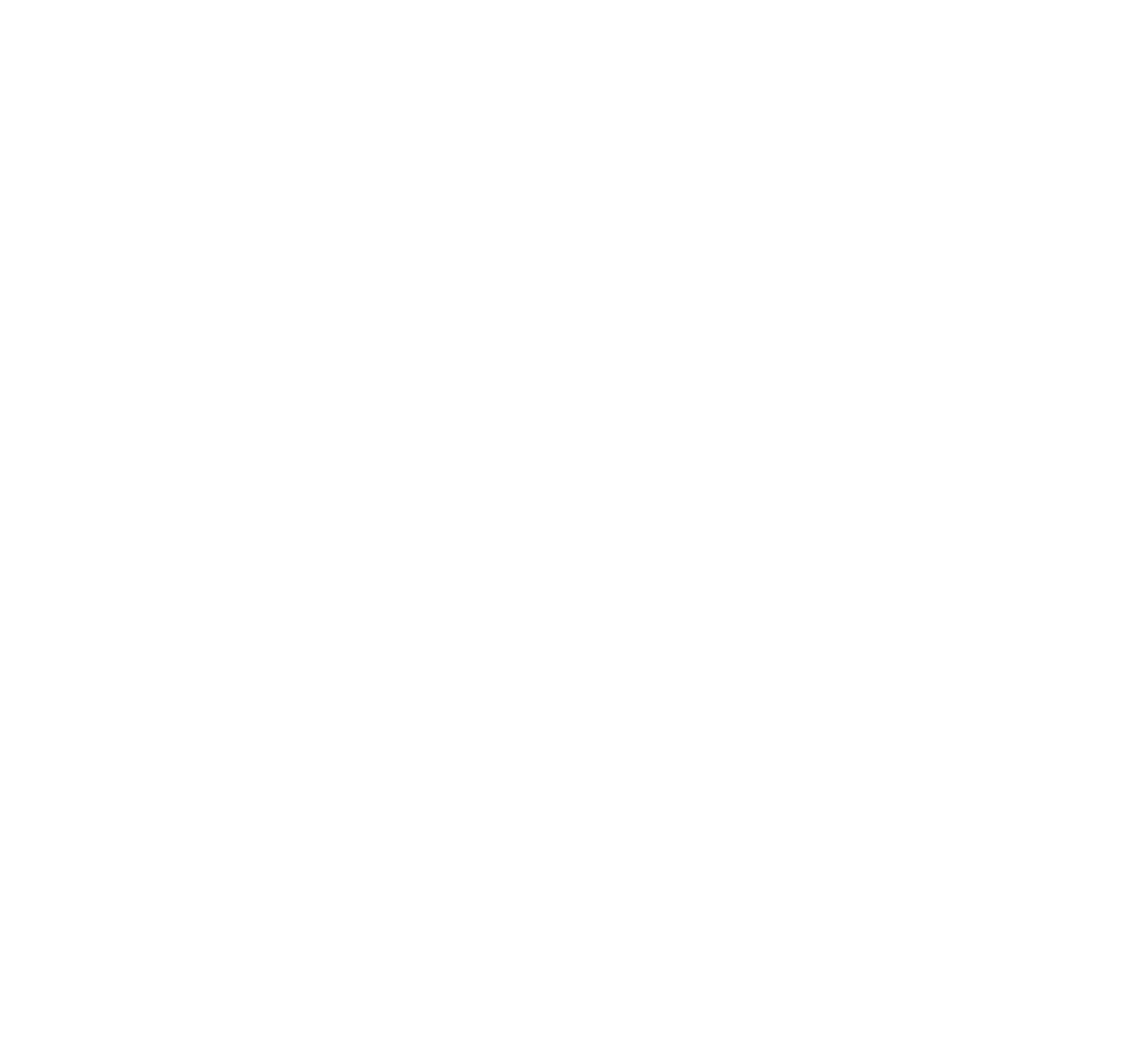
Production Lead Time Reduced by 40-60% at Rivne Plant of High-Voltage Equipment
Rivne plant of high-voltage equipment reduced the manufacturing lead time of orders by 40-60% with the IT-Enterprise ERP system implementation
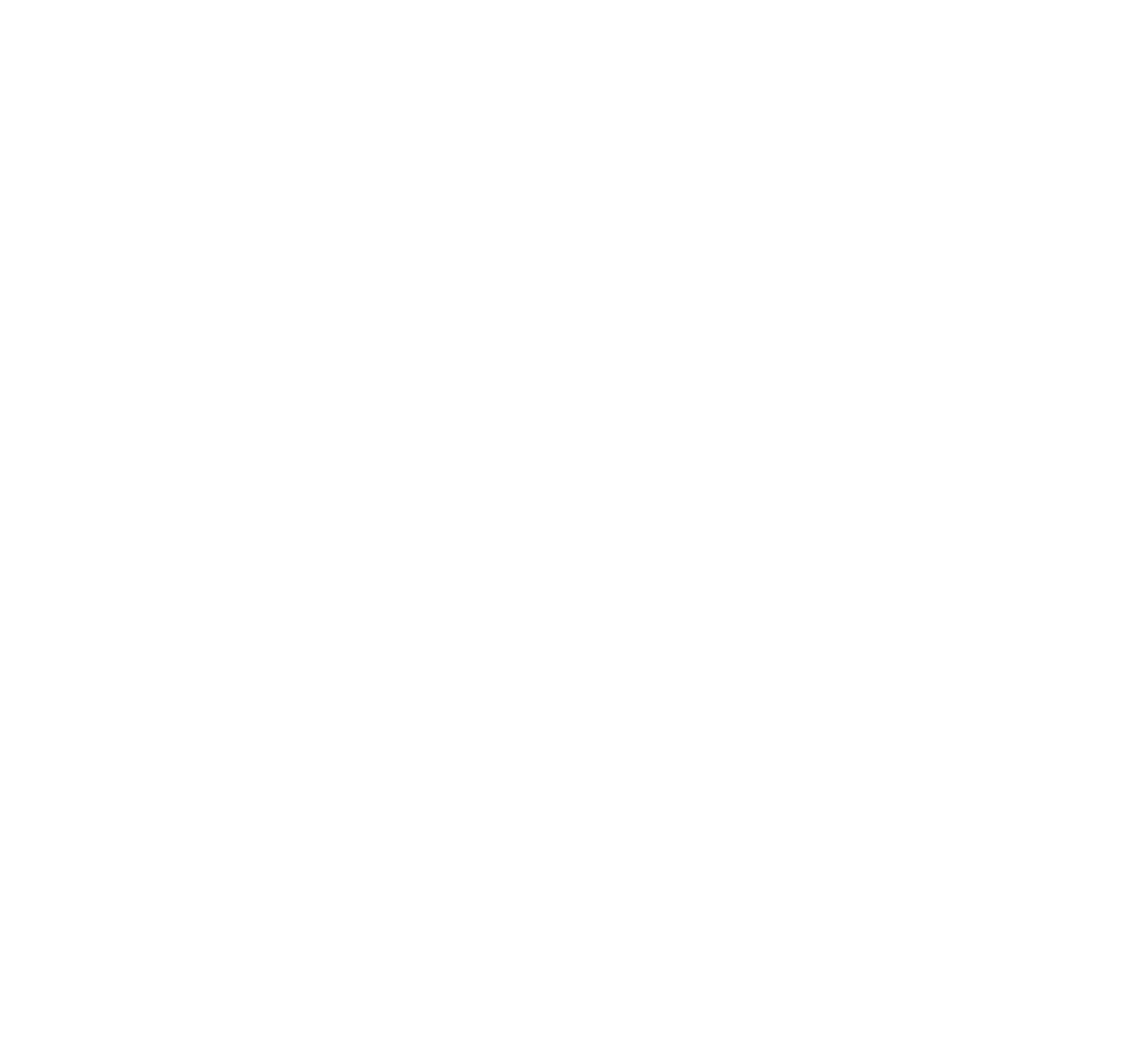
Industrial giant Zorya-Mashproekt digitalization reduced product development time by 1/3 and helped to enter new markets
Having an integrated ERP system from IT-Enterprise, Zorya-Mashproekt has successfully implemented a large-scale digital transformation project, switched to electronic document management and become more globally competitive.
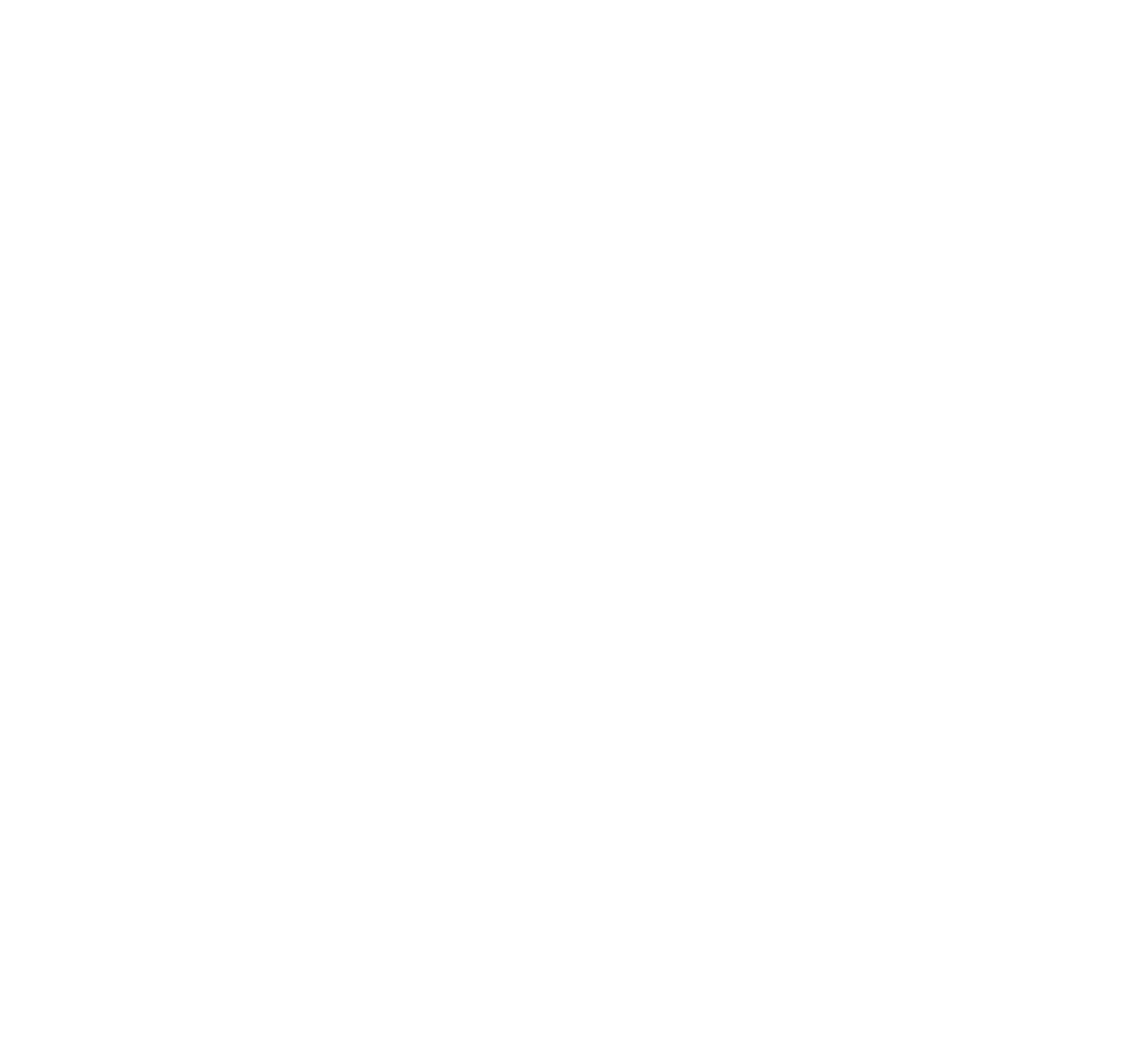
Modern accounting tools allowed to detail cost structure
Implementation of the modern management ERP functionality in the industrial-construction group "Kovalska" for 4 months
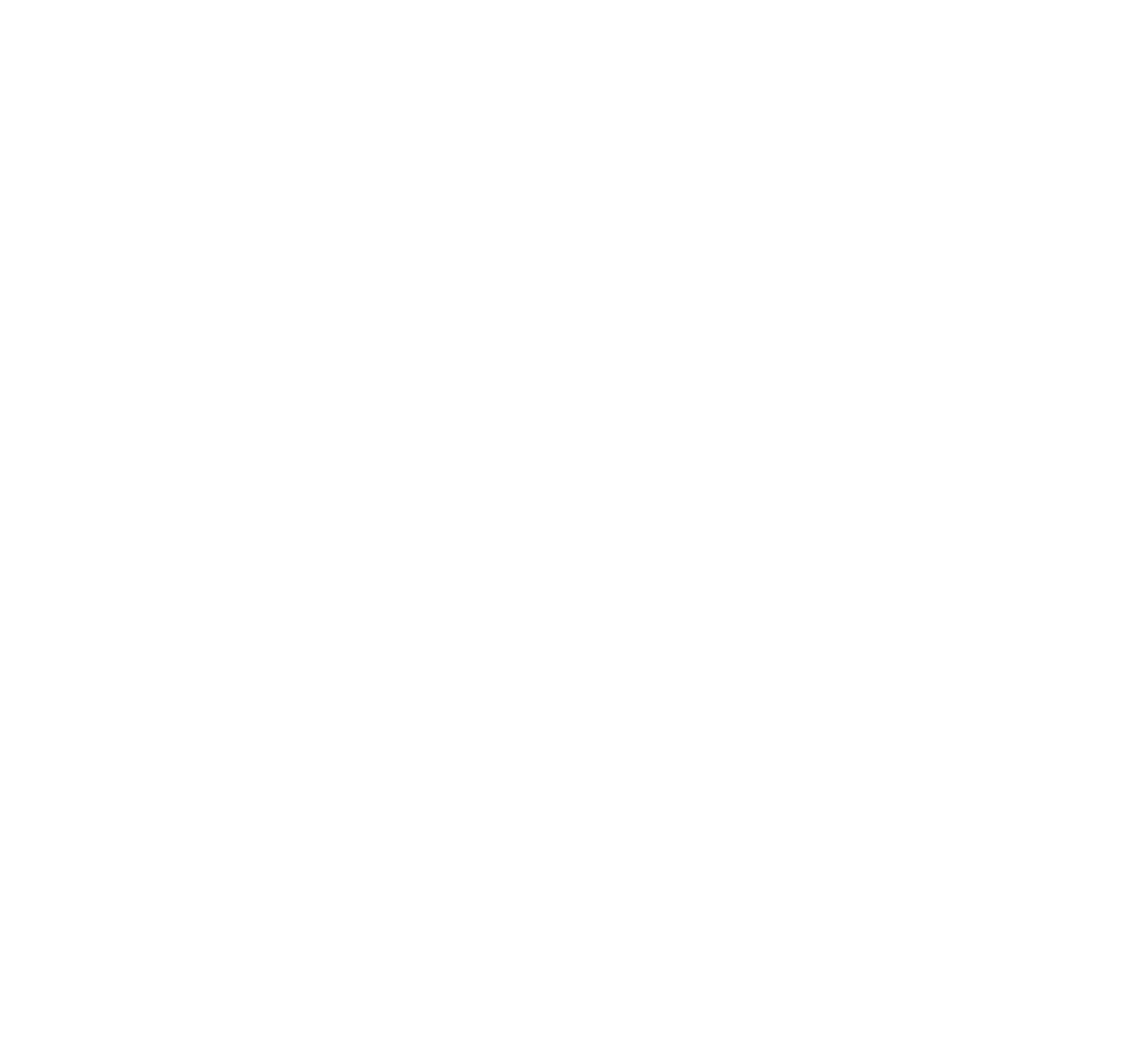
Unified accounting system for a large distributed manufacturing enterprise
How IT-Enterprise team has created a unified accounting system in the large distributed enterprise "Antonov"
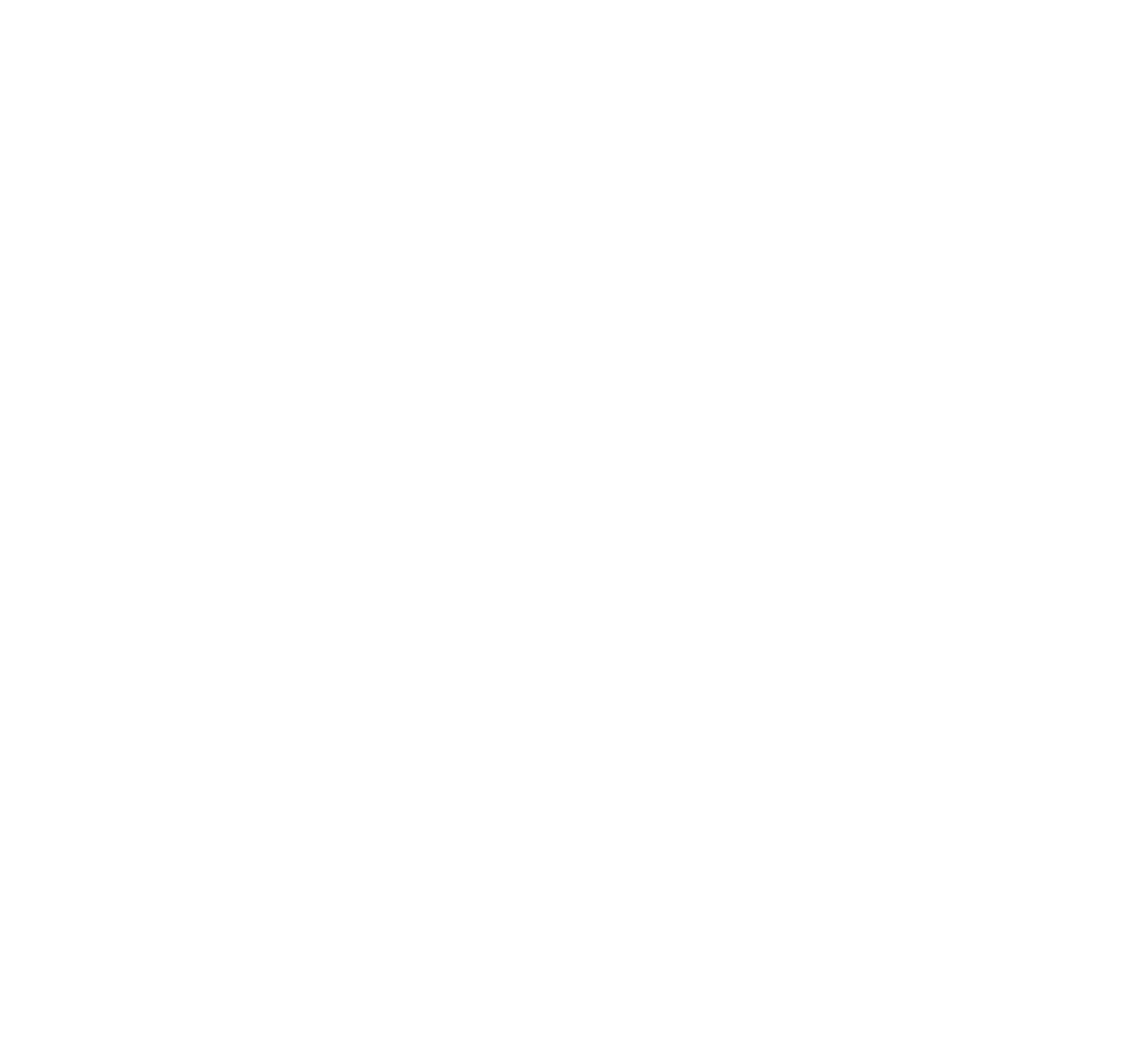
Lviv Locomotive Repair Plant doubled throughput and achieved 15-20% faster repair cycle
Similar to most machine-building enterprises, the Lviv Locomotive Repair Plant aimed to increase production throughput while ensuring a certain level of repair work profitability. In addition, the project team faced the task of improving the plant division’s manageability that required an integrated system covering all key departments and services.
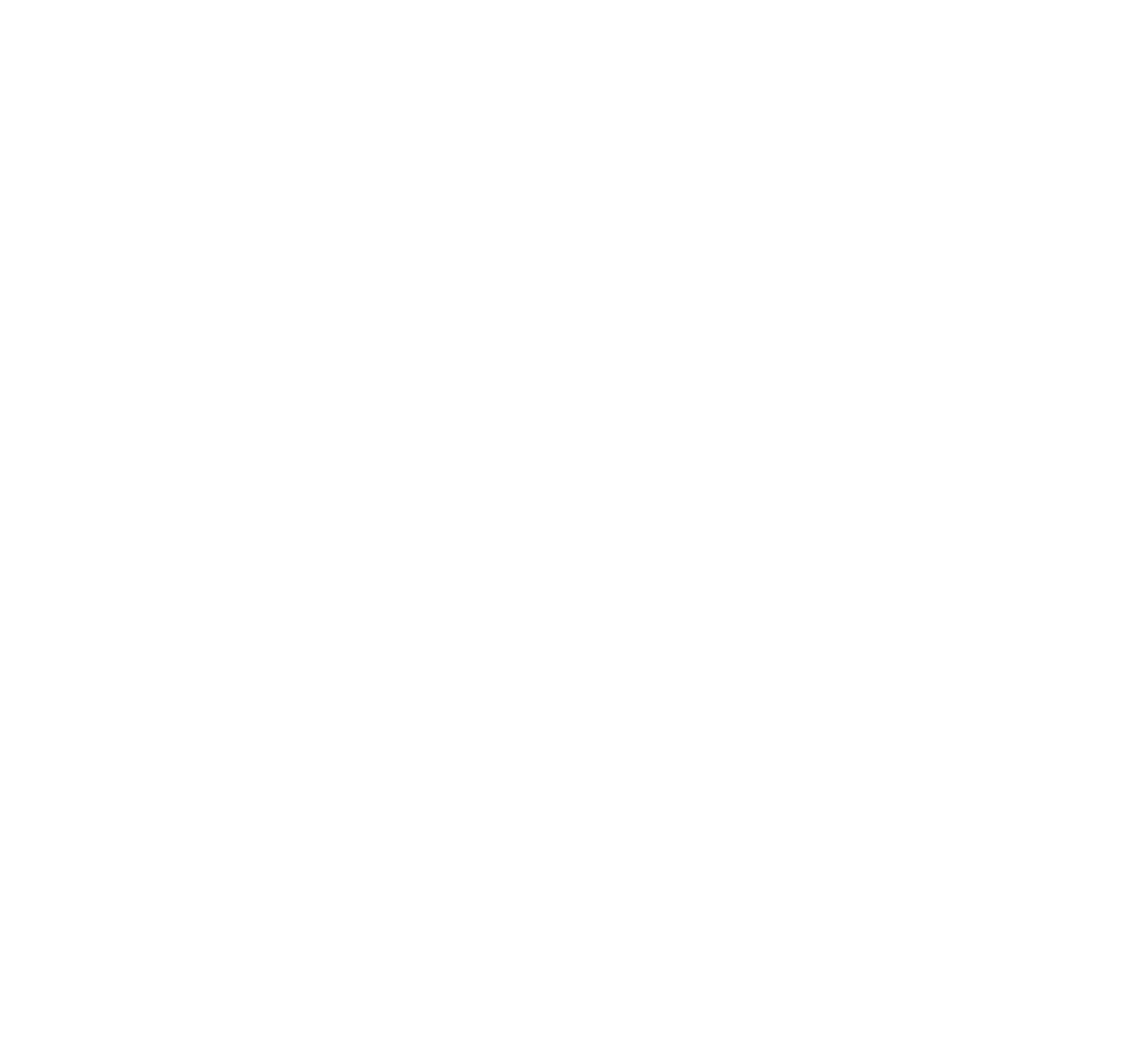
30% Bigger Output with Operational Production Control at Zorya-Mashproekt
How a science-and-production complex of gas turbines "Zorya" - "Mashproekt", one of the world's leaders, has achieved an increase of 30% of production output through operational control of production
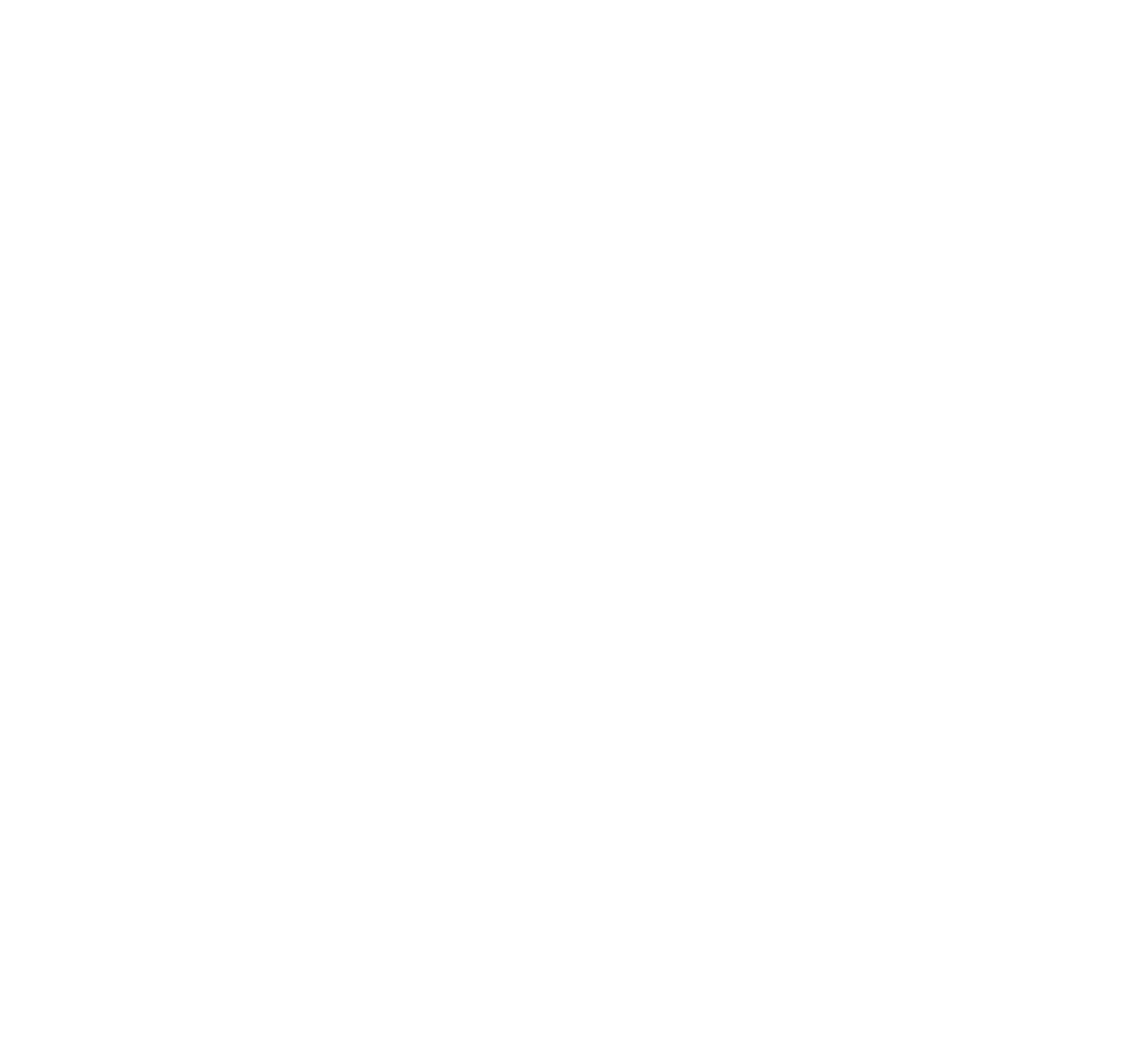
SmartFactory by IT-Enterprise – a platform for sustainable development of Interpipe
Due to the implementation of the SmartFactory by IT-Enterprise, industrial holding "Interpipe" reduced the storage costs of materials, reduced the risk of breaking schedule routine and failure of the orders timing, improved the rhythm of the production, and significantly reduced equipment downtimes.